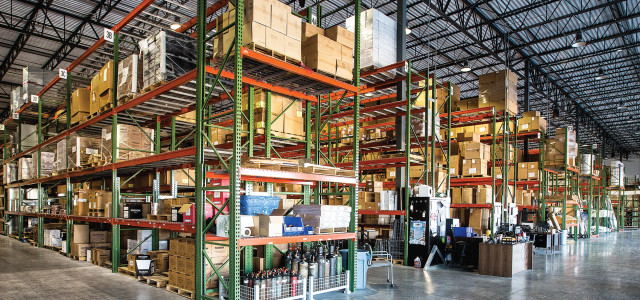

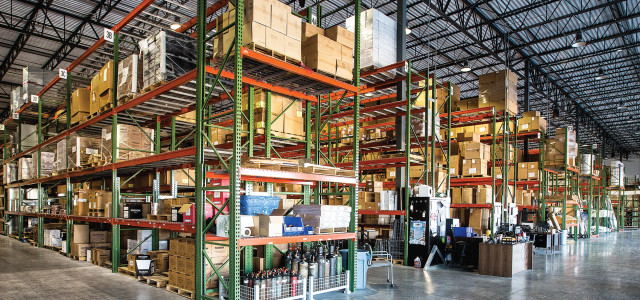
Based on the tidal wave of demand for new industrial space, Robert Brown predicts another banner year for commercial contractors that struggled during the construction drought. “In the last 12-18 months, the demand for industrial warehouses has increased significantly,” he says. “But since nothing’s been built for quite awhile, the vacancy rate for dock-high space is virtually nil.”
This scarce supply offers abundant opportunities for Brown’s tilt-wall and concrete construction business, GCM Contracting Solutions, Inc. (GCM) in Fort Myers. “Years ago, ceilings with clear heights of 20 feet were the norm in our market,” says Brown, GCM’s owner and president. “These days, warehouses with dock-high space and 35-foot ceilings are what users want most,” but also what they’re least likely to find on the market.
According to Brown, explosive population growth and the proliferation of online shopping have prompted an urgent need for new warehouses and distribution facilities in Southwest Florida and beyond. Despite the 10 million square feet of new industrial space currently being built statewide, there remains a dearth of newer space in our market. It’s a void that GCM is well qualified to fill.
Established in 1988, GCM provides concrete construction and design/build services to countless commercial clients in this market and beyond. From the outset, the company has advocated the tilt-wall method of construction to deliver attractive, high-quality buildings, frequently ahead of schedule and under budget. In addition to warehouses, distribution centers and manufacturing facilities, GCM’s project portfolio includes shopping centers, casinos, hotels, hospitals, schools and prisons, among others. In Lee County, some of its most visible, large-scale projects include Chico’s World Headquarters, the Miromar Design Center, the Alico Business Park, Croci International manufacturing facility and much of Gulf Coast Town Center.
A Diverse Portfolio
Although the majority of its tiltup and concrete work involves large commercial structures with open floor space and high ceilings, GCM has also completed security walls and sound barriers, multi-family housing and single-family homes, as well as buildouts, remodels and renovations. On occasion, GCM has redesigned and reconstructed warehouse-style space to be used for an entirely different purpose. For instance, in 2012 the company converted the 17,000sf former Picture Factory in south Fort Myers into The Law Offices of Kevin Jursinski, complete with conference rooms, a kitchen and other amenities.
Other recent projects further reflect the broad scope of GCM’s capabilities and include:
- Victor Distributing (Fort Myers)
Using tilt-wall construction, it took GCM just over six months to complete a 60,000sf facility for Victor Distributing, an HVAC wholesale distributor. The facility, located on Treeline Avenue in the Jetport Commerce Park, opened in mid-2015 and contains warehouse space with a mezzanine for storage, as well as some showroom and office space.
- Caliber Collision Body Shop (Bonita Springs)
With more than 18,700sf, the Bonita Springs facility is the newest of several Caliber Collision shops in Lee County. Texas-based Caliber is the nation’s largest vehicle collision repair company, boasting more than 450 state-of-the-art locations in 16 states. GCM completed the Bonita facility in November and is currently building another Caliber Collision shop in Tampa.
- Mosaic Arena (Arcadia)
After years of planning, GCM recently began work on the 7,796-seat Mosaic Arena in DeSoto County, adjacent to the Turner Agri-Civic Center. When completed later this year, the $9+ million facility will be the new home of the Arcadia All Florida Championship Rodeo and will provide the community with a modern venue for special events.
Waterfront Pioneer
Some of GCM’s most impressive accomplishments are closer to the coast, where Brown says the company is “changing the face of the marine industry,” in part by replacing dilapidated metal dry storage facilities with tilt-up structures that are more durable, economical and attractive. “We were the first to do tilt-up in the marine industry, and, in fact, the first in the world to do an all-concrete dry-stack marine storage facility,” Brown adds. As a result, marinas and boat storage facilities have become a significant focus for the company.
Brown says that concrete tilt-wall is ideal for building large waterfront structures, particularly in Florida. In addition to being rated for wind (up to 150 mph) and fire (four hours between boat bays), concrete boat barns and other marina structures are easy to maintain and can be attractively designed and decorated to blend with their surroundings.
Aesthetics were extremely important when GCM was building the Hamilton Harbor Marina in Naples. Initially, residents of nearby upscale neighborhoods opposed construction of the 110,000sf, all-concrete dry-stack boat storage facility, fearing what a massive industrial building would do to property values. Ultimately, they were thrilled with the finished product, which looked more residential than commercial. The beautiful, state-ofthe- art facility garnered GCM a 2008 Summit Award for Best Design/Build Project.
GCM continues to work its tilt-up magic at marinas throughout Florida. In December, it completed construction of Rose Marina on Marco Island, which had operated since 1969 and needed a complete overhaul. The project included construction of a two-story marina office complex, additional boat storage, and a new shipping and receiving center for the adjacent ship’s store, which was also renovated. The marina’s new concrete boat barn can now accommodate more and larger vessels — 142 boats of 43+ feet.
One of GCM’s most ambitious projects to date is Gulf Star Marina on Fort Myers Beach, next to Doc Ford’s waterfront restaurant. There, Brown is working with marina owner Todd Carroll, a managing partner of Carroll Properties, to replace the existing metal boat barn with a facility unlike any the marine industry has seen before.
Game-Changing Technology
Renderings of the new, state-of-theart Gulf Star Marina show an attractive, modern building with architectural details that belie its industrial purpose. At 28,500sf it will be slightly larger and much taller than its aging, metal predecessor. When completed, the 103-slip dry-stack facility will be able to accommodate vessels up to 40 feet. But the most impressive aspect of the building lies behind its tilt-up walls: a first-of-its-kind automated storage and retrieval system that Brown predicts will revolutionize the marina and boat storage industry.
“It’s pretty phenomenal,” he says. “This will be a game changer.”
Made in Germany, the automated system has been used in European warehouses for years and is similar to the type of machinery used in automated distribution centers. However, this is the very first time it has been adapted for boat storage and retrieval.
Engineering and installing the innovation is costly, and the building is being designed around it. However, Carroll says the advantages of the new technology make it a worthwhile investment. “This automated system addresses the two main challenges at Gulf Star: a small site and our inability to accommodate larger boats,” says Carroll.
He says the new system will increase capacity without expanding the building’s footprint because it doesn’t use a forklift to store and retrieve boats. “If you don’t need room for a forklift to swing and turn around, you can whittle the width of the drive-aisles substantially and use that space for storage,” Carroll says.
He notes that automated retrieval and storage is much faster than with a forklift and less likely to damage boats during transit because it’s so mechanically precise. It can also handle heavier loads at greater heights, enabling the heaviest boats to be stored on top.
Pending final county approvals, construction of the new marina could get underway later this year and take about 12 months to complete. Carroll says he’s looking forward to the improvements. “Once the system is operational, I think everybody’s going to want to come and see it in action,” he says. “I’m excited that we may be the first marina to have this technology.”
Brown says that in addition to marinas, automation could be applied to other projects in places where developable land is scarce and pricey. For example, in an area like Fort Myers Beach where there’s limited parking, an automated parking garage would allow cars to be stacked, thereby accommodating more of them in a smaller space.
“You’d literally drive your car into a vestibule, get out, prepay with a credit card and go about your business while your car is automatically moved and stored,” says Brown. “Then when you’re ready to go, you’d use a phone app to alert the system to retrieve your car for pickup so it would be ready and waiting for you.”
Prospects and Possibilities
When he isn’t identifying innovations and opportunities to help GCM’s existing clients, Brown is working to attract new ones. “Most of our clients are either moving into the market and looking for space or moving up in the market with a relocation or expansion.”
Currently, GCM is bidding on a number of industrial warehouse projects ranging from 30,000sf to upwards of 140,000sf, although most are in the 50,000-100,000sf range. Brown noted that all are near I-75 in south Fort Myers and slated to start construction this year. Prospective clients include a beverage facility, furniture warehouse and distribution centers.
Brown says he expects to expand GCM’s staff this year to meet the company’s growing workload.
“Fort Myers is starting to mature as a commercial market,” says Brown. “We’re still behind markets like Tampa and Miami, but we’re coming along.”